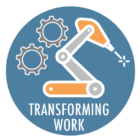
In a 2012 post entitled Low pay driving job vacancies I posited that the reason manufacturers had a shortage of skilled trades workers was low pay, not a skills shortage. That post featured a New York Times Magazine article by Adam Davidson entitled Skills don’t pay the bills. Davidson wrote:
The secret behind this skills gap is that it’s not a skills gap at all. I spoke to several other factory managers who also confessed that they had a hard time recruiting in-demand workers for $10-an-hour jobs. “It’s hard not to break out laughing,” says Mark Price, a labor economist at the Keystone Research Center, referring to manufacturers complaining about the shortage of skilled workers. “If there’s a skill shortage, there has to be rises in wages,” he says. “It’s basic economics.” After all, according to supply and demand, a shortage of workers with valuable skills should push wages up. Yet according to the Bureau of Labor Statistics, the number of skilled jobs has fallen and so have their wages.
In a recent study, the Boston Consulting Group noted that, outside a few small cities that rely on the oil industry, there weren’t many places where manufacturing wages were going up and employers still couldn’t find enough workers. “Trying to hire high-skilled workers at rock-bottom rates,” the Boston Group study asserted, “is not a skills gap.” The study’s conclusion, however, was scarier. Many skilled workers have simply chosen to apply their skills elsewhere rather than work for less, and few young people choose to invest in training for jobs that pay fast-food wages.
This, of course, is what most of learned in introductory economics. That, except in the rare case when you run out of a natural resource, market economies cannot have structural supply/demand imbalances. That price is what brings the two into balance. In labor markets wages and benefits (and to some degree working conditions) are the price. So that the way to deal with too few skilled trades workers is to raise wages.
Nearly a decade later Michigan manufacturers are still complaining there is a shortage of skilled trades workers. To determine whether those are now high-paid blue collar manufacturing jobs, I looked at the May 2020 Michigan occupation and wage estimates for production occupations from the Bureau of Labor Statistics. I looked at the average yearly wage and used the University of Michigan RSQE $47,000 middle class household of three threshold.
First the big picture. Contrary to conventional wisdom, blue collar manufacturing jobs are no longer high paying. The May 2020 average wage for Michigan’s 3,924,000 payroll jobs was $53,390. For the 399,000 production (blue collar manufacturing) jobs the average pay was $42,470. So blue collar manufacturing jobs were ten percent of all Michigan payroll jobs and their average wage was 80 percent of the statewide average.
More specifically, here are the production occupations with an average yearly wage of $47,000 and above and how many people they employed.
- Engine and other machine assemblers: $53,690, 7,850 workers
- Model makers, metal and plastic: $68,510, 600 workers
- Model makers, wood: $69,280, 50 workers
- Pattern makers, metal and plastic: $57,250, 270 workers
- Tool and die makers: $57,040, 9,910 workers
- Layout workers, metal and plastic: $50,830, 80 workers
- Chemical plant & system operators: $58,110, 100 workers
- Chemical equipment operators and tenders: $57,630, 4,780 workers
- Computer numerically controlled tool programmers: $55,300, 2,120 workers
- Furnace, kiln, oven, drier and kettle operators and tenders: $47,080, 1,010 workers
- Jewelers and precious stone and metal workers: $51,370, 480 workers
- Stationary engineers and boiler operators: $65,160, 510 workers
That is it! 12 occupations. Totaling 27,760 jobs. 27,760 is less than one percent of all Michigan payroll jobs.
Given all the attention it gets it is worth noting that welders are not on the list. The average wage for May 2020 Michigan welders was $42,370.
The occupation list does not include production occupations in utility plants and oil and natural gas extraction, which most of us would not think of as manufacturing. The data are for 40 hours a week, 52 weeks a year. So it does not include overtime pay or bonuses.
The evidence continues to make a strong case that if there is a structural shortages of manufacturing skilled trades workers the prime cause is low pay and benefits and unattractive working conditions. That the primary answer to this chronic labor shortage is market based: employers increasing price and improving working conditions.